In questo articolo:
- Shaping plastic or shaping its market?
- Painting and aesthetics: the purchase that passes also through pleasure
- Starting situation: the challenge for Movingfluid
- The test: IR+ADIA for liquid paint curing on plastic
- Conclusions: IR+ADIA advantages in paint curing on plastic
- IR+ADIA and non-metallic materials: application potentials and market perspectives
Shaping plastic or shaping its market?
For manufacturing companies, an industrial plastic painting process that is versatile and competitive in terms of quality, times and costs can be the winning weapon to establish oneself in lots of sectors.
In effect, in an increasingly customer-oriented market, the ability to effectively respond to the request to produce resin products, with different colours and shades and in a wide range, represents an important commercial differentiation element.
Curing of non-metallic surfaces presents a series of problems related to heat sensitivity of the material themselves.
In industrial plastic painting, for a correct curing of liquid paints on surfaces that cannot be exposed at drying temperatures above 70/80°C, curing times of some tens of minutes are required.
To overcome such long and unprofitable times, in many cases the choice of manufacturers is alternatively one of the following:
- Colouring raw material resin for small elements in the production phase
- Apply coloured films or coloured panels on resin surface through industrial pressing processes.
However, both of those solutions encounter considerable operational and economic limits.
If on the one hand they production capacity not very flexible, on the other they prove to be very onerous activities in the case that there was a need to produce “just in time” or to offer a choice of colours on dozens of different pantones. Those ones not uncommon situations in the current, competitive, demanding and frenetic marketplace.
Here comes the Movingfluid’s challenge.
In the case story that you are about to read, we will show you how our engineering consultancy team has come to develop a universal solution capable of taking the leap for all those companies involved in the painting of plastic material and that are able to grasp it from the start.
Thanks to the use of IR+ADIA technology, we were in effect able to obtain every of the following advantages at the same time:
- Perfect curing of liquid paint on resin surfaces (aesthetic quality, guarantee of the reliability of the result and resistance)
- Drastic reduction in production times
- Reduction in spaces for the same production levels
- Extreme flexibility thanks to the possibility of setting the processes on small and large batches according to the needs in real time.
If it looks extraordinary to you, it actually is.
Assure the advantage on your competitors.
Ask immediately for a study applied to your case on the use of IR+ADIA.
Painting and aesthetics: the purchase that passes also through pleasure
Painting of plastic parts has become an indispensable ally of the reference market, for issues related to the resistance of treated parts, as well as for aesthetic reasons.
For example, think of what added value in the automotive market represents the possibility to have a specific colouring in combination with the body colour and in general harmonising colours between the various parts of different materials, in addition to the fact that, the more the coating will be characterised by lustre and brilliance, the greater will be the ability to please, attracting the final customer to the purchase.
Surface painting, when is well done, is also able to delete small production defects, thus limiting waste.
Furthermore, from a functional point of view, external plastic in vehicles must be protected from atmospheric agents to which it is daily exposed (humidity, UVA rays) that would lead to deterioration and consequent rapid embrittlement (improvement of the durability requirement).
The same reflections in terms of benefits and opportunities can be extended to many other areas. For example, think of furniture and all those objects that have entered our everyday life, from household appliances to technology, where design is essential and the colour is often able to determine client’s choice by itself.
Liquid painting, used specifically for this test, exploits paint chemical and physical properties to create numerous visual and tactile effects, giving particular finishes to the treated pieces and, at the same time, protecting their surface with an anticorrosive layer, also resistant to chemical agents.
Starting situation: the challenge for Movingfluid
To obtain results that fall into the desired quality standards, industrial plastic painting process requires compliance with specific procedures, before pieces can be downloaded, checked, packaged and labelled.
Here comes the challenge accepted by Movingfluid: considerably reduce the times and spaces required for paint curing on resin surfaces, to make the production process quick and economically advantageous.
The following are the phases and related processing times normally required by the curing process of paints on plastic materials, in which the temperature must necessarily be kept below 80°C, to not generate expansions and deformations in the treated pieces:
- Application of neutral primer
- First curing of neutral primer: 5-10 min.
- Waiting for neutral primer drying
- Application of coloured paint
- Second curing at 80°C in oven: 15 – 20 min.
- Piece cooling: 10 min.
Estimated total cycle time: about 30 – 40 min.
The test: IR+ADIA for liquid paint curing on plastic
Used paints:
Used components, in alignment with our clients’ specifications:
- Bi Primer, water-soluble paint based on acrylic resins by Sherwin-Williams – WB white Inverpur (code 39304)
- Bi Topcoat, water-soluble paint based on acrylic resins by Sherwin-Williams – WB Inverpur/R blue RAL 5011 (code 48222)
Water-based or water-soluble paints now represent a market standard, guaranteeing performance and results that are comparable, if not superior, to traditional solvent-based paints in terms of range and quality, while fully respecting the environment.
The method applied and the results obtained are to be considered of universal value, therefore replicable in the presence of processes that involve the use of paints with the same characteristics, produced by other brands.
Procedure followed:
- Inverpur Primer Application
- Inverpur Topcoat Application on wet surface, without waiting for the curing phase to be completed.
- Curing phase with the use of IR+ADIA technology. Infrared radiation propagates thorough electromagnetic waves, developing heat only when it meets the surface to be treated, allowing significant energy savings.
- Cooling through adiabatic system, based on exploiting the ability of air to absorb vapour in order to lower the temperature.
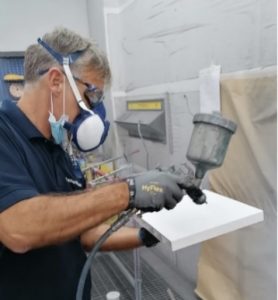
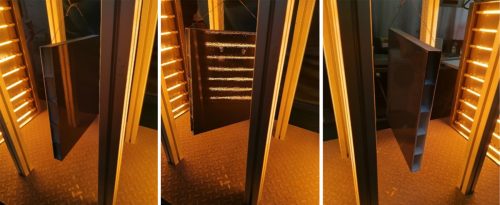
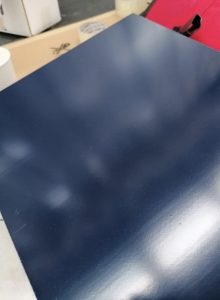
Paint curing through IR+ADIA technology | Paint curing in traditional ovens | Saved time with the use of IR+ADIA technology | % of improvement (production increase) |
|
Paint curing time | 5 min. | 20-30 min. (primer curing included) | 15-25 min | + 75% |
Cooling | 2 min. | 10 min. | 8 min. | + 80% |
Total | 7 min. | 30-40 min. | 20-33 minòl./b> | + 77% |
We are experts in fluid handling.
If you have any problem or want to improve YOUR process, just call us.
Conclusions: IR+ADIA advantages in paint curing on plastic
IR+ADIA, the Movingfluid’s technology that combines paint curing inside infrared ovens with an adiabatic cooling system, has proven its effectiveness even on non-metallic surfaces. This system has thus proved to be perfectly suitable for being inserted in industrial painting cycles of plastic or any non-metallic material which, due to its physical characteristics, cannot be exposed to high temperatures without undergoing deformation.
The following are the main advantages that the manufacturer who intends to adopt the IR+ADIA curing system will immediately benefit from:
- Higher production flexibility thanks to the use of liquid paints
- Considerable reduction in production times
- Reduction in the space required for production cycle (less space required for executing the entire process including packaging).
- Reduction in the energy required for production compared to gas ovens for paint curing, with a subsequent reduction in CO2 emissions.
- High quality, with perfect adhesion and total absence of possible surface defects, such as the formation of bubbles or pitting.
All Movingfluid’s solutions follow a working method that goes beyond the ordinary. Discover hereby all characteristics of our approach.
IR+ADIA and non-metallic materials: application potentials and market perspectives
New horizons for industrial painting of assembled products
A technology like IR+ADIA is destined to change forever the approach to industrial painting on the market, marking its future.
Just think of the implications and possibilities opened up by a paint curing process now applicable to a very wide range of elements, no longer stressed by exposure to too high temperatures.
This means that preassembled components in different materials can be treated together, unifying painting interventions in a single moment, initially separated at different levels of the production process. In this way, painting can be inserted at the end of what would become a single production process.
Benefits in terms of optimisation of the time required, movement of pieces, use of manpower, space occupation and energy saving are exponential.
Which industries could benefit from IR+ADIA?
For time saving, productivity increase and workspaces optimisation, IR+ADIA represents an indispensable solution for all those companies whose production process involves a painting phase, even for small batches or “on-demand” batches, thanks to its versatility.
Particularly, in addition to the operational and economic advantages outlined above, IR+ADIA offers the achievement of an optimal quality level in the painting of non-metallic materials, which is essential for all those sectors where aesthetics combined with resistance represents an added value.
IIR+ADIA paint curing technology is applicable to all plastic materials (carbon, multi-resin, ABS, polypropylene, …) as well as to various supports, such as wood.
Think of the possible implications in the furniture sector, where wood and plastic materials are frequently coupled to satisfy every taste need and where design, colouring and gloss are essential must-haves.
Potentials of IR+ADIA technology make the approach to the plastic painting process easier, generating greater profit. Among the activities that can derive essential benefits from the IR+ADIA technology we mention:
- Painting and surface treatment service companies for third parties
- Automotive
- Recreational nautical sector
- Household appliance manufacturers
- Indoor and outdoor furniture
- Lighting
- Construction of doors and armoured doors
- Furnishing accessories and design objects
Paradoxically, we could meet the desire expressed by Andy Warhol, who is so attracted to plastic that he longs for an entire world made of this material: “I love Los Angeles. I Love Hollywood. They are beautiful. They are both made of plastic, but I do love plastic. I want to be plastic!”
Today, unlike the years in which Andy Warhol lived, we are aware of how important it is to contain the production and waste of this material.
All the more reason, enhancing and preserving it with quality protective treatments, using non-polluting paints and reducing the use of energy seem to us due acts of responsibility.
IR+ADIA technology has no limits of application.
Do you want us to test its benefits in your production process?
- Alstom [1]
- ARO Ingersoll Rand [1]
- Automotive [8]
- Brembo [2]
- Case History [13]
- Cast iron brakes [1]
- Ceramic [2]
- Chemical [3]
- chemical mixer [1]
- Chemistry [2]
- Cleaning [1]
- cleaning industrial machinery [1]
- Dilution [1]
- Dosage [4]
- Dust [1]
- Extrusion [3]
- Finishing [1]
- Fluid handling [3]
- Fluids [2]
- Food [1]
- Freni in ghisa [1]
- Gases [3]
- Glue [2]
- Henkel [1]
- Industrial Painting [4]
- IVECO [1]
- Know-how [2]
- Körber Tissue [2]
- Lamborghini [2]
- Liquid paint [1]
- Liquids [6]
- LPR [1]
- Market news [4]
- mixing chemicals [1]
- Nikola [1]
- Oenology [2]
- Oil & Gas [1]
- Paint [2]
- Paper [2]
- Paper converting [1]
- Paper industry [2]
- Powder Coating [1]
- Powders [1]
- pump test bench [1]
- Raw material producer [1]
- Saipem [1]
- Spraying [5]
- Streparava [1]
- SuperSix [1]
- Tissue [3]
- Tissue converting [2]
- Toscotec [1]
- Trail [1]
- Transfer [7]
- Verniciatura industriale [3]