In this article:
- A new approach to the solution: problem identification
- Toscotec: from Italy, the paper that goes round the world
- How to win a speed race
- An idea of automation
- A satisfaction that becomes standard
A new approach to the solution: problem identification
In the paper industry production chains, industrial bonding operations are often an essential part of the process.
Industrial bonding is a seemingly ancillary activity. Yet, that very moment can be the cause of production downtime with drastic consequences, if dispensing technical adhesive or an operator spreading it manually encounters a difficulty.
The availability on the market of increasingly sophisticated technical adhesives, designed for specific uses, cannot, in fact, stop a mechanical problem from occurring, such as an uneven application or no material coming out from a nozzle if the glue has dried out.
In this case history we will show you how our solving mishaps found a way to fully automate the industrial bonding process and through this, make the whole system more efficient.
A solution that derives from the identification of the problem by our engineering consultants.
In fact, Movingfluid was compared to a system with no apparent special requirements or need for optimisation, with the challenge of looking for something that could be improved. Challenge won!
The added value of Movingfluid‘s intervention in this shadowing consists precisely in having been able to identify the most critical part of the whole bonding process – dangerous and entrusted to man – that with the highest risk of lost productivity.
Intervening at this stage meant that the customer was assured of completely autonomous machinery with increased safety and reduced consumption. A true novelty that, with the Toscotec signature, is determined to characterise the production future of the tissue industry.
Toscotec: from Italy, the paper that goes round the world
With Toscotec we are in the presence of one of the most prestigious Italian brands in the tissue converting industry.
Founded in 1948 in Lucca, the core of Italy’s paper district, the Toscotec group today employs approx. 180 people, with sales offices in China and North America, and has an annual turnover of around 150 million Euro. The recent acquisition by the German Voith GmbH group consolidates a success story, opening the door to new markets and growth opportunities.
In detail, Toscotec specialises in the design and production of turnkey projects, complete lines, plant reconstructions and spare parts for the tissue, paper and carton industry. Systems characterised by state-of-the-art technology and extensive customisation options, which aim for maximum production efficiency, with reduced consumption and operating costs and a guarantee of top-quality finished products. The commercial value of a complete Toscotec line can be close to 10 million Euro.
The work of these complex machines consists in converting paper pulp from lignocellulosic fibrous material to virgin paper sheet. The final product is then wound around a mother reel about 5 metres wide, 60 metres long and weighing several tonnes, to be intended for domestic use – after further processing.
It is precisely the bonding of the final flap of this cumbersome reel, which is necessary to achieve a closure that avoids unwinding, that is the focus of Movingfluid‘s improvement.
Against a backdrop of such technological excellence, this single out-of-control detail does not escape the watchful eye of our engineering consultants who, having focused on the weakness, immediately devise an automatism to ensure the system’s uninterrupted efficiency.
Does your system have any problems?
We will be able to bring out more.
How to win a speed race
AHEAD is the paper processing plant that Movingfluid is called upon to analyse.
Entirely made up of Toscotec machines, AHEAD spans a length of approximately 100 metres and is fully customisable, thanks to its flexible configuration, perfectly adaptable to customer requirements and operating conditions.
Its production capacity varies between 80 and 250 tonnes of paper per day, generated at the impressive speed of 1,500-2,200 metres per minute.
For every hour of its operation, three rolls of paper require manual intervention by an operator to be cut, glued by hand and removed from the roll. One roll every 20 minutes. A frequency that prevents the operator from focusing on any other activity, as he cannot be distracted from this repetitive, dangerous and highly responsible task.
A real speed race for us solving mishaps!
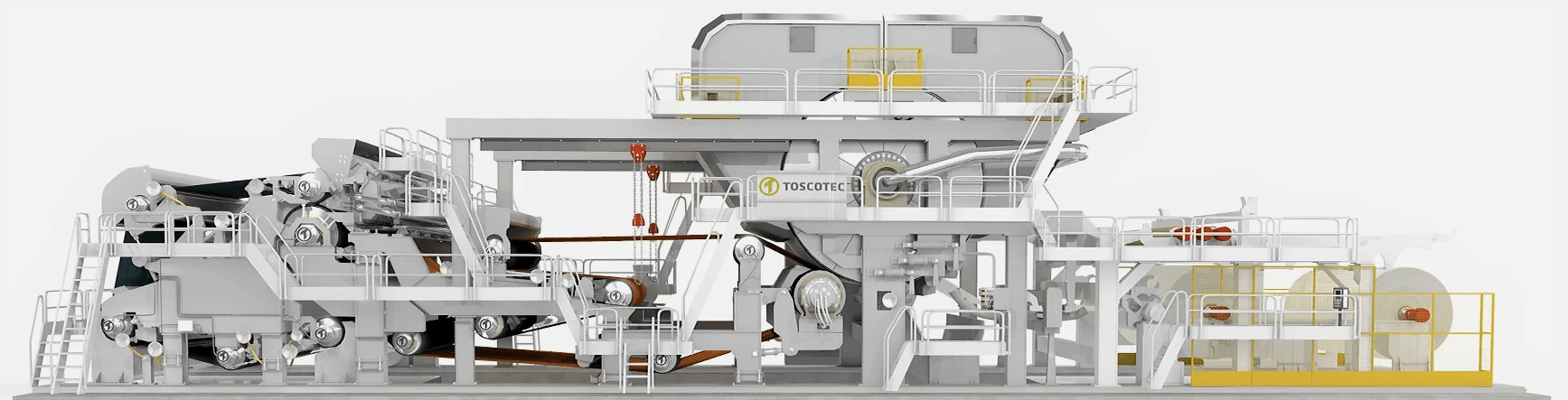
The situational analysis carried out by Movingfluid on the operating AHEAD system revealed the following main critical issues:
1 – Personnel safety
Safety problem for the operator, identified when his presence is required in order to:
- operate a blade to cut the paper on the rolling machine. As a result of this action, the reel, which has been made independent of the shear, continues to wind on itself with a highly dangerous imprinted rotational force and a mass of several tons to steer, which is very difficult to manipulate. Therefore, all these operations need to be carried out as slowly as possible.
- spread a layer of glue on the end flap of the paper – by spraying the adhesive substance with a gun connected to a 10-litre pressurised tank – to close the roll and send it to the next stages of packaging, shipping and sales.
2 – Production efficiency
Such an application proves to be highly inefficient, as well as unreliable. Should something go wrong during the above-mentioned operation, the production and economic repercussions would be huge. A clogged gun, a dirty tank and a badly mixed product are enough to interrupt the whole cycle.
With energy-intensive machines like this, where the rollers have to be constantly heated to very high temperatures, a production stop is a huge mishap. Avoiding it is priceless.
This is why the complete automation of the industrial bonding process designed and implemented by Movingfluid was a much-appreciated bonus in this production context.
To upgrade your system in an ingenious way
An idea of automation
Our pumping expertise allowed us to come up with an idea that could overcome both of these limitations. ARO® pumps, for which we have been distributors and promoters for over 30 years, have once again proved to be valuable allies in the configuration of an effective and customised system.
We therefore offered a test-based industrial bonding solution, following the famous ‘feasibility test’ introduced to the market 30 years ago: “If it does what I say, the machine is yours. Otherwise, it’s mine.”
This is an approach that Movingfluid has always taken towards its customers, anticipating all design and prototyping costs.
From a semi-automatic bonding system…
Movingfluid identified the fine-tuning of a glue spraying system as a priority, which would guarantee optimal preservation of the adhesive substance, preventing the fluid from drying out, while ensuring uniform density and free of deposits at the bottom.
For this reason, Movingfluid introduced a stainless steel ARO® 4:1 pump with a 40-litre tank and pneumatic stirrer into the production cycle. This made it possible to:
- reduce the possibility of the liquid drying out to zero – a particularly frequent occurrence in hotter countries
- reduce the frequency of top-ups – offering a range of several days (glue required: 7.5 KWh per day. Top-up frequency: once every 5 days).
A hand gun was then connected to the pump, which was able to spray more efficiently on the reel and ensure perfect bonding (glue used: Ecofix Voith, with viscosity 2,300 cPs and density 1.1).
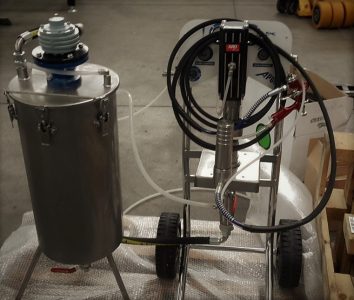
Following the positive outcome of this first test based on using a semi-automatic reel gluing system, we offered Toscotec the possibility of reaching a further level: fully automated process, excluding the presence of the operator.
A perspective welcomed by the customer, who immediately grasped its full potential.
…to full automation
Therefore, Movingfluid built a fully automated industrial bonding system consisting of a closed stainless-steel cabinet, containing:
- an ARO® 45:1 stainless steel pump for spraying glue
- an ARO® 4:1 stainless steel pump for water washing
- a 100-litre tank with a pneumatic stirrer
- a Pneumatic Control System (SMC), capable of actuating the two pumps independently and the stirrer, remotely controlled from the Toscotec control cabin.
- a DS pressure regulator, manually adjusted
- two automatic spring-loaded guns, coupled and placed on a common base to allow immediate water washing of the nozzle after spraying. These guns, fitted on a high-speed mechanism, are capable of covering up to 2,700 mm of horizontal spray in about 1.6 seconds.
Not a minor aspect: the system was fitted with a safety system. Approaching or working on it under such high pressures would expose the operator to a high risk. For this, the circuit has been set up to allow a pressure reduction, if necessary.
Lastly, the entire system was provided by us with specially drafted CE manuals in Italian and English, as Movingfluid‘s support to its customers is always guaranteed.
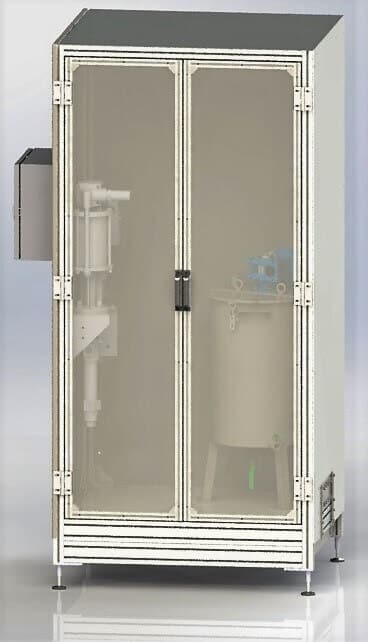
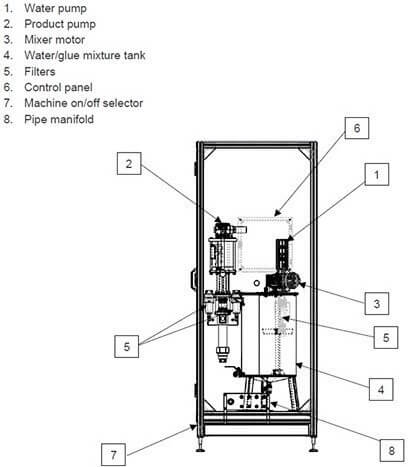
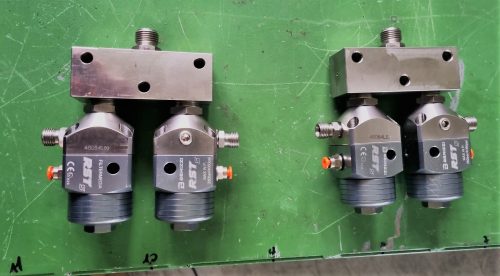
A satisfaction that becomes standard
The automatic bonding system for paper rolls suggested and implemented by Movingfluid for Toscotec significantly increased the quality and speed of operations, successfully applying about 160 cc of glue in 1.6 seconds, on a 2,600 mm wide horizontal surface 3 times per hour!
These are the main advantages:
- increased safety, without an operator in the vicinity of a rolling device in operation
- higher quality, thanks to the reliability and consistency of the automatic spraying operation
- reduced consumption and zero downtime: exact knowledge of the amount of glue used for each cycle allows constant control of the level and filling of the device in advance, without waste and downtime.
- remote operation: the supervisor of the main machine also controls the spraying
- reduced maintenance requirements: the system is self-cleaning, with a minimum amount of water required (300 cc/h = 7.2 litres per day, to be disposed of on site).
- reduced manual work time
The highly satisfied customer standardised the solution: the automatic spraying system will be offered to Toscotec customers as an accompaniment to each new processing line.
This is an added value that many companies in the paper and tissue industry are recognising, considering that in 2021 there are already 7 automatic bonding systems in demand and for 2022 there are numerous orders.
Once again our solving mishaps overcame a great challenge – putting themselves on the line and never approaching a situation with standard solutions to sell.
On the contrary: it is perhaps the solutions provided that will become new standards for the customer: when you look to the future, it is difficult to turn back.
Does your company also have a story to tell
and a future to be created?
We can be at your side with the right additional idea.
- airless painting [1]
- Alstom [1]
- ARO Ingersoll Rand [1]
- Automotive [8]
- Brembo [2]
- Case History [13]
- Cast iron brakes [1]
- Ceramic [2]
- Chemical [3]
- chemical mixer [1]
- Chemistry [2]
- Cleaning [1]
- cleaning industrial machinery [1]
- Dilution [1]
- Dosage [4]
- Dust [1]
- Extrusion [3]
- Finishing [1]
- Fluid handling [3]
- Fluids [2]
- Food [1]
- Freni in ghisa [1]
- Gases [3]
- Glue [2]
- Henkel [1]
- Industrial Painting [4]
- industrial tile painting [1]
- IVECO [1]
- Know-how [2]
- Körber Tissue [2]
- Lamborghini [2]
- Liquid paint [1]
- Liquids [6]
- LPR [1]
- Market news [4]
- mixing chemicals [1]
- Nikola [1]
- Oenology [2]
- Oil & Gas [1]
- Paint [2]
- Paper [2]
- Paper converting [1]
- Paper industry [2]
- Powder Coating [1]
- Powders [1]
- pump test bench [1]
- Raw material producer [1]
- Saipem [1]
- Spraying [5]
- Streparava [1]
- SuperSix [1]
- tile [1]
- tile painting [1]
- Tissue [3]
- Tissue converting [2]
- Toscotec [1]
- Trail [1]
- Transfer [7]
- Verniciatura industriale [3]
- vortex hydra [1]