In this article:
- Automatic IBC washing: processes that become sustainable
- Automatic IBC tank washing: the higher gear for many sectors
- Tank washing: what needs to change
- Applied solution: an extraordinary washing experience
- No longer without: the advantages of automatic IBC washing
- The results achieved: let’s count
IBC automatic washing: processes becoming sustainable
If you use IBC tanks in your facility, you’ve definitely realised that you need to optimise the IBC tank washing operations so that they can be reused, saving as much time and money as possible required of a task which actually generates no direct profit.
This case history shows you how precisely the IBC washing process automation has improved our customer’s efficiency so as to reduce the costs of this activity by 71%, considerably affecting the margins of the entire process.
So is it really possible to optimise the tank recovery procedure so as to generate greater profit compared to the entire production cycle? The result we achieved was called a miracle by the customer himself, a brand among the main manufacturers of fertilisers in Germany, who would’ve been hard pressed to believe to go that far when he expressed his needs: “We can no longer allow an added low-value job to generate so many costs and waste, as well as to be way too unhealthy and dangerous for operators”.
The figures show that by shadowing our reference helped them to save over 40,740 € a year by solely intervening on the tank washing process.
A challenge won by providing added value in many perspectives:
- Reduced washing costs
- Quicker procedures
- Better quality
- Enhanced operator safety
A solution that can easily be implemented in any production context, with minimum impact on space (in the end even less is needed!) without turning the layout of the production lines upside down.
The same experience can be applied to many sectors of reference. Perhaps yours too.
What are you waiting for?
Get in touch with us for a free consultancy.
That’s the first step to take.
Automatic IBC tank washing: the higher gear for many sectors
IBC tanks are used to hold and transfer liquids in a variety of production environments. The chemical, pharmaceutical, building, farming industry, as well as the winemaking and food sector – just to mention a few – use IBC tanks to store liquid substances.
Perfectly suitable for convenient transport and making the best of spaces thanks to their cubic shape, the tanks are thus filled with glue, adhesives, inks, cosmetics, oils and foodstuff liquids. Substances intended to be used later on in the facility itself, for example in the production cycle, or to be delivered to an outside customer with the “deposit” formula.
Once emptied, the IBCs need thorough washing before being reused, whether being filled again with the same product or with different types of liquids.
IBCs are an eco-friendly choice, introducing us to the culture of reuse, without generating waste or producing extra containers, with the implicit expenditure of energy or use of new raw materials.
It was our duty to shadow our customer in this environmentally sustainable decision for the environment, even making costs sustainable. It’s not a job to do, but a bet to win.
Protagonists of this case history are 1000 litre IBC tanks in high density and high molecular weight polyethylene, protected by a galvanised steel tubular cage and secured on a platform. In 90% all of the situations, this is the type of IBC container used in companies, offering low-cost plastic, versatile and relatively easy to handle.
Instead of plastic, you may also choose IBC stainless steel tanks. Definitely more expensive when bought and disposed of, tanks made of this material are sturdier, more antistatic, fireproof, healthy and safe. Their use becomes paramount when used with certain substances.
The solution of the IBC tank washing automation which we are about to show you is perfectly applicable both to plastic and stainless steel containers, with configurations aimed at guaranteeing in both cases the drastic reduction of times and costs, at the same time guaranteeing greater quality and safety for operators.
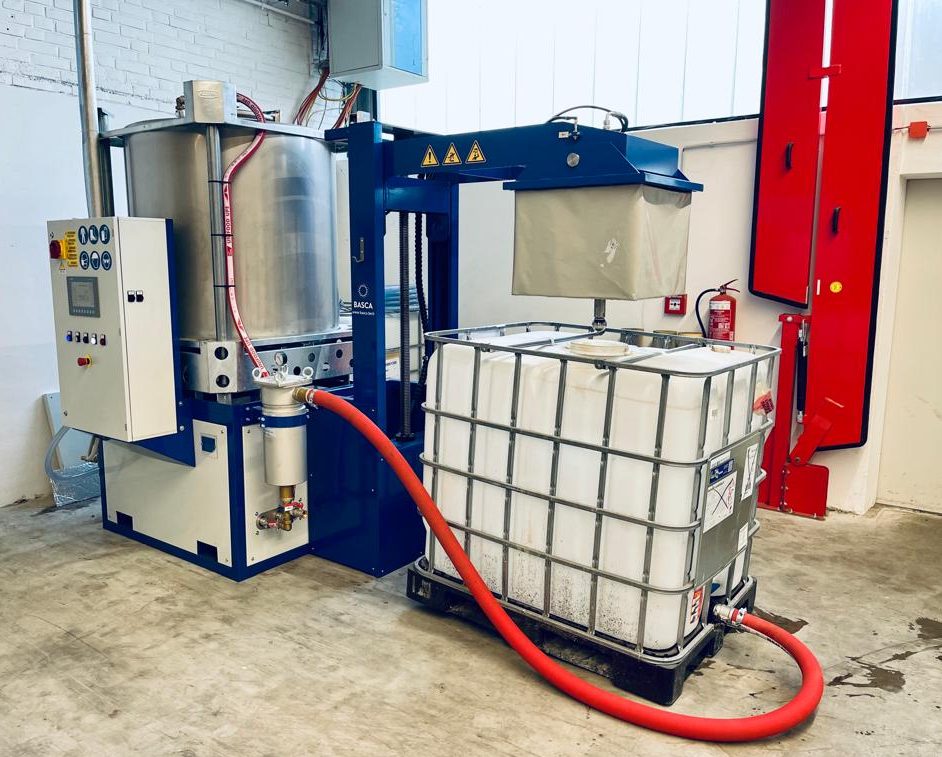
Tank washing: what needs to change
When we meet customers, this is a situation that they describe and that just can’t go on.
At the company, about 10/15 IBCs need to be washed every day. The job is normally carried out manually by an operator spending at least 4 h a day, outside, to wash IBCs with a pressure washer.
Manual washing is expensive and dangerous: it’s not easy to manually handle 50 kg, movements are not ergonomic and the grip is not safe. These issues are combined with often treacherous work conditions, with wet and slippery floors.
Besides being a dirty, uncomfortable and unhealthy job, washing tanks with a pressure washer is by no means ecological, as it generates abundant waste. We’re talking about as many as 800 litres of wastewater a day to be disposed of. Valuable water, thrown away uselessly, making it impossible for the company to be within sustainable corporate parameters and to take advantage of possible tax benefits.
Last but not least, manual washing of tanks is absolutely uneconomic for our customers.
Let’s count: at a corporate cost of about 20 €/h, IBC washing labour costs the customer 19,200 €/year. The resulting disposal costs add up to 38,400 €/year, for a total of 57,600 €/year.
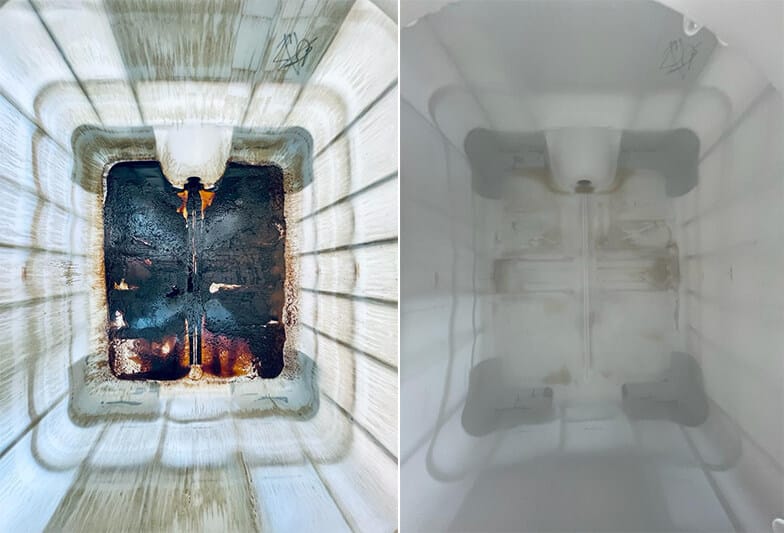
Whatever the size of your company,
the efficiency of its processes is enhanced by making this call.
Applied solution: an extraordinary washing experience
Movingfluid supported the customer with a situational analysis, including cost and feasibility analyses, in the end suggesting to insert a machine made specifically to automate tank washing.
An efficient, cost-effective and highly environmentally friendly solution, with zero impact on existing work processes.
Based on current conditions and needs expressed, our engineers determined the most effective configuration of the device to provide the best results.
The following are the distinctive features of the automatic IBC washing system implemented for our customer:
- high-pressure washing at 150 bar
- quick cleaning cycle, in only 3 minutes
- total elimination of chemical agents: the technology applied only uses hot water at a temperature of 50°C, guaranteeing perfect cleaning while respecting the environment.
Furthermore, if the company needs to sanitise the container making it suitable for example for contact with foodstuff, a final rinse with chemical sanitizer can be added.
How does the automatic tank washing system work?
An operator places the IBC to be recovered next to the machine. Having selected the wash recipe on the touch panel, he/she can lower the head using the specific command and start the cycle. The washing head starts to spin and at the same time sprays 50°C washing water that circulates at 150 bar.
When the wash is over, the machine automatically switches to rinsing and injects clean water into the system. The rinse water is then suctioned from the circuit.
Clearly, labour time is considerably reduced, with just one operator working 1 hour a day.
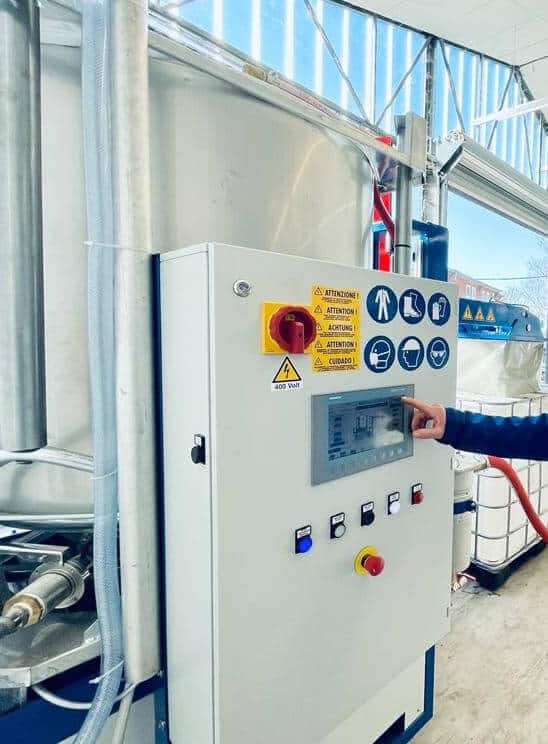
No longer without: the advantages of automatic IBC washing
In addition to the considerable economical benefits, which we will analyse in detail below, there are a host of reasons to choose an automatic IBC tank washing system.
A choice which knows no alternatives, if you consider the following essential features of the system:
- User friendly: simplified management of the wash operations. The operator only needs to place the tank on the machine and to remove it at the end of the wash cycle, setting the parameters on the control panel by hand.
- Versatile: the machine has several wash programs (eco wash, standard wash, intensive wash). This makes it possible to choose the most appropriate treatment depending on the degree of filth and the type of substance to be removed.
- Quick and effective: a single operator quickly manages all the operations of the system: more IBCs will be ready for use in the same amount of time.
- Enhanced quality: the strong, controlled and multidirectional water jet, not subject to the inevitable deficits characteristic of manual operation. The wash recipes are optimised for type of filth.
- Safe for persons: manual washing is no longer sustainable. This system zeros health risks and issues, eliminating the exposure of workers to chemical products and to dangers such as the slippery work environment.
The operator only needs to position the tank and to remove it at the end. All performed within a protected area and no longer outdoors, as the dirty water will no longer be spilled onto the ground but collected to be put back into circulation.
- Sustainable: reduction of water consumption with resulting containment of the wastewaters generated of 80%. Instead of being released into the environment intended for disposal, the water is recycled for the continuation of automatic washing. A concrete aid to reduce costs for purchasing and disposing of washing liquids, thus streamlining operations and improving the results.
Immediate and tangible operational advantages.
Let’s get to the point. How much do you actually save?
The results achieved: let’s count
When all is said and done, the savings which our customer took advantage of are:
Labour and wastewater disposal costs: reduced by 75%
Total washing costs: reduced by 71%
Each detail in the following chart:
DESCRIPTION | COST | UNIT VALUE | TOTAL YEARLY VALUE | |
MANUAL WASHING |
Labour cost for manual washing |
20 €/h |
4 h/day |
€ 19,200 |
Wastewater disposal cost |
0.2 €/l |
800 l/day |
€ 38,400 |
|
Total |
€ 57,600 |
|||
AUTOMATIC WASHING |
Labour cost for manual washing |
20 €/h |
1 h/day |
€ 4,800 |
Wastewater disposal cost |
0.2 €/l |
200 l/day |
€ 9,600 |
|
Cost of power for machine use |
0.2 €/KWh |
20 KWh per day |
€ 960 |
|
Cost of consumables and spare parts |
€ 1,500 |
|||
Total |
€ 16,860 |
|||
SAVINGS |
€ 40,740 |
|||
ROI |
4 MONTHS |
Can you believe these numbers?
Let’s count together.
For any questions,
Do you know all the advantages of Movingfluid solutions?
Do you know that it’s us who are investing for you, economically going out on a limb for your project and if we don’t meet your goals, it doesn’t cost you anything?
Do you know that our advice has no commercial strings attached? We don’t need to sell products: we choose the best solution for you on the market, keeping up-to-date on all the novelties in the pumping sector.
If you’re curious to know all that we can do for you, find out here!
And don’t forget that… we are “mishap-solvers” by nature!
- Alstom [1]
- ARO Ingersoll Rand [1]
- Automotive [8]
- Brembo [2]
- Case History [13]
- Cast iron brakes [1]
- Ceramic [2]
- Chemical [3]
- chemical mixer [1]
- Chemistry [2]
- Cleaning [1]
- cleaning industrial machinery [1]
- Dilution [1]
- Dosage [4]
- Dust [1]
- Extrusion [3]
- Finishing [1]
- Fluid handling [3]
- Fluids [2]
- Food [1]
- Freni in ghisa [1]
- Gases [3]
- Glue [2]
- Henkel [1]
- Industrial Painting [4]
- IVECO [1]
- Know-how [2]
- Körber Tissue [2]
- Lamborghini [2]
- Liquid paint [1]
- Liquids [6]
- LPR [1]
- Market news [4]
- mixing chemicals [1]
- Nikola [1]
- Oenology [2]
- Oil & Gas [1]
- Paint [2]
- Paper [2]
- Paper converting [1]
- Paper industry [2]
- Powder Coating [1]
- Powders [1]
- pump test bench [1]
- Raw material producer [1]
- Saipem [1]
- Spraying [5]
- Streparava [1]
- SuperSix [1]
- Tissue [3]
- Tissue converting [2]
- Toscotec [1]
- Trail [1]
- Transfer [7]
- Verniciatura industriale [3]