In this article:
- Aesthetics and design in plants: a must in industry
- Versatility, precision, smoothness. This is how we were awarded the tender
- Lamborghini and Movingfluid: the service ad personam that wins over the customer
- New challenge for our “Sirs Wolves”: obstacles to overcome
- How we transformed problems into just as many solutions
- Final results: goals achieved in record times
Aesthetics and design in plants: a must in industry
In the context of upgrading the painting processes in the Lamborghini plant, Movingfluid successfully responded to an essential need for the customer: make new 100% custom paint booths, completely like the pre-existing ones inside the customer’s paintshop.
This is a requirement of many manufacturers, especially in the OEM sector, where the visual and functional alignment between machinery represents an essential factor inside the establishment.
Often the brands themselves dictate the aesthetic configurations and parameters: the entrepreneur is not always free to choose whether or not to do it. Customisation is ever more necessary.
This is why total customization is one of the services we offer. This is how we meet our customer’s need of making solutions designed with pre-established components in predetermined areas, taking care of all stages from study to the finished product.
This alongside Lamborghini is a case history that demonstrates how the capability of Movingfluid technicians of meeting the customer’s requirements knows no limits: the harder it is, the more it’s our job. In our perspective, the strongly binding conditions of this project appeared as a challenge to be overcome.
The result was beyond our expectations. The paint booths designed by Movingfluid were inserted in the previous production systems with an exemplary aesthetic continuity. As regards functionality and performance, the new paint booths proved to be better than the previous ones due to their extraction and air circulation capacity. A must for the customer.
But before quantifying the results in detail, follow us in this new challenge won by our “mishap solvers”.
Problems finishing your plant?
Supplier disappeared? Machinery discontinued?
Guarantee that your machinery has visual and functional continuity with custom solutions.
Versatility, precision, smoothness. This is how we were awarded the tender
In the month of April 2020, Lamborghini launched a tender for the design and implementation of three paint booths to be installed in their paintshop, alongside just as many pre-existing booths.
More specifically, the paint booths in question are located at the end of the production process, in the post curing stage. Liquid paint is used inside the booths, applied by operators always present inside the booth spraying the car body. A high-precision manual job, to meet the very high aesthetic requirements of the luxury segment of the automotive industry.
The paint booths made take care of the finishing needs of the new Urus versions, models with ever lighter elements – in carbon and composites – and configuration options of the ad personam bodywork.
Lamborghini considers the protection of their workers’ health inside the paint booth as a sine qua non: results concerning technical performance will be worth nothing if not accompanied by a proven adequacy of the work environment in accommodating operators in safety conditions, to be guaranteed through adequate ventilation.
The following are some of the binding demands of the tender:
- integration of the new paint booths with the previous plant, in spaces designed by the previous manufacturers (with considerable constraints in terms of reachability and the need to make fumes exhaust chimneys, inexistent in the assigned spaces);
- total aesthetic conformity to the surrounding environment: keeping the inside and outside look and feel of the paint booths the same as the context;
- looking for better filtering and air circulation performance than the pre-existing paint booths.
Movingfluid was awarded the tender thanks to its considerable skills, know-how and proven experience in fluid movement.
Top-notch professionalism, together with the small size of our structure compared to that of big contractors in the sector allowed us to offer a focused, flexible and quick service.
A precise response to the customer’s requirements, with no exceptions.
A tailor made service for Lamborghini.
You need to upgrade your painting system but you have aesthetic constraints and small spaces?
Lamborghini and Movingfluid: the service ad personam that wins over the customer
Founded in 1963, Automobili Lamborghini is based in Sant’Agata Bolognese, in the province of Bologna, where it manufactures among the most coveted super sports cars in the world.
In 2017 Automobili Lamborghini launches Urus, the first Super SUV, creating a new luxury car segment and establishing a point of reference in terms of power, performance, driving dynamics, design and daily usability. A real gem for all of those who have a passion for engines and new technologies.
With 165 dealerships worldwide, in 2021 Lamborghini’s car sales grew for the ninth straight year, establishing a new record. With a 43% increase in orders, the prestigious car brand went from 5,750 to 8,205 cars delivered worldwide. Among these, 5,021 are the Urus.
The demand for luxury cars is growing exponentially, and with it, the amount of possible variants and customisations, to satisfy the tastes of each individual customer. We’re talking about a sector where a car is passion and passion needs to express emotion. The final quality and aesthetic appearance are fundamental.
Just like the exceptional service of delivering on time. The customer can’t wait. Production cannot slow down. To meet the demands, the Emilia-based company has grown exponentially regarding the sizes of the factory and the enhancement of the production lines.
New challenge for our “Sirs Wolves”: obstacles to overcome
Execution speed and the capability of overcoming every obstacle. Like in an obstacle course, Movingfluid is ready to go at the starting blocks to tackle any design and execution issue and to quickly turn it into an advantage for the customer.
The following are the needs expressed by the prestigious automobile brand and the relative difficulties:
- Integration of the new booths inside of the workplace, without visibly breaking with pre-existing plants.
The previous system, built at the same time as the establishment itself, is fitted on a floor with metal grille, assembled 7 m high.
It features an extraction and centralised air circulation system, which cannot be used for the three new paint booths. Therefore, when making the new booths, an independent and autonomous ventilation system must be made at the same time without affecting the pre-existing infrastructure.
- Implementation of new paths on the ground to transport the bodies to the paint booth.
The supply includes the extension of the tracks which the LGV (Laser Guided Vehicles) drive on, used to automatically transport the car bodies into the booths. The acceptable alignment precision error is +/- 5 mm.
The difficulty in managing this alignment depends on the fact that the floor structure is made of steel sheets, which in turn rest on a metal scaffold.
- Transport of materials to assemble the paint booths.
The material for assembling the paint booths can only reach the work deck through a single narrow passage 7 metres high: a 2.5 x 6 m wide trapdoor.
- Compliance with the indicated deadlines, obliged by production times.
The three paint booths the tender refers to are intended for the finishing of carbon and lightweight material parts, a treatment not provided in the pre-existing booths.
Since our work is close to the last intended deadline for the start of this production, Movingfluid absolutely needs to respect the following worksite dates:- end of March 2021 – start of work
- within and not beyond May 10, 2021 – delivery
How we transformed problems into just as many solutions
Movingfluid engineers made a duct system under the floor of the work decks, 7 m high, to resolve the problem linked to air extraction.
To this purpose, a duct system was designed which, assembled at that height, then merges into an extraction system mounted above the floor. A new chimney was then connected to it vertically, built by making a hole in the roof.
The construction of a perfectly working flue is a focal point for the correct execution of the project. The fumes must be captured before reaching the painter’s breathing area, to protect their health. Afterwards, the gaseous emissions must be filtered, to then be ejected outside the plant, in compliance with standards in force for exhausts into the atmosphere.
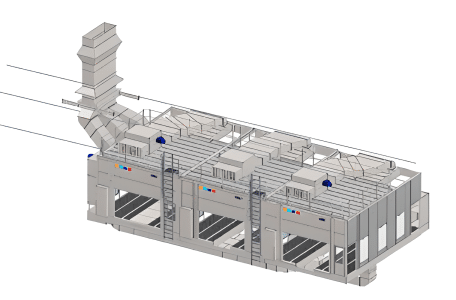
To facilitate the exhaust of fumes and guarantee the constant effectiveness of extraction, a stabilising windproof system was set up outside of the plant.
You must consider that the system’s construction area is subject to high gusts of wind, frequently changing direction. This makes it necessary to create a safe and protected chimney structure, which guarantees reliable operation.
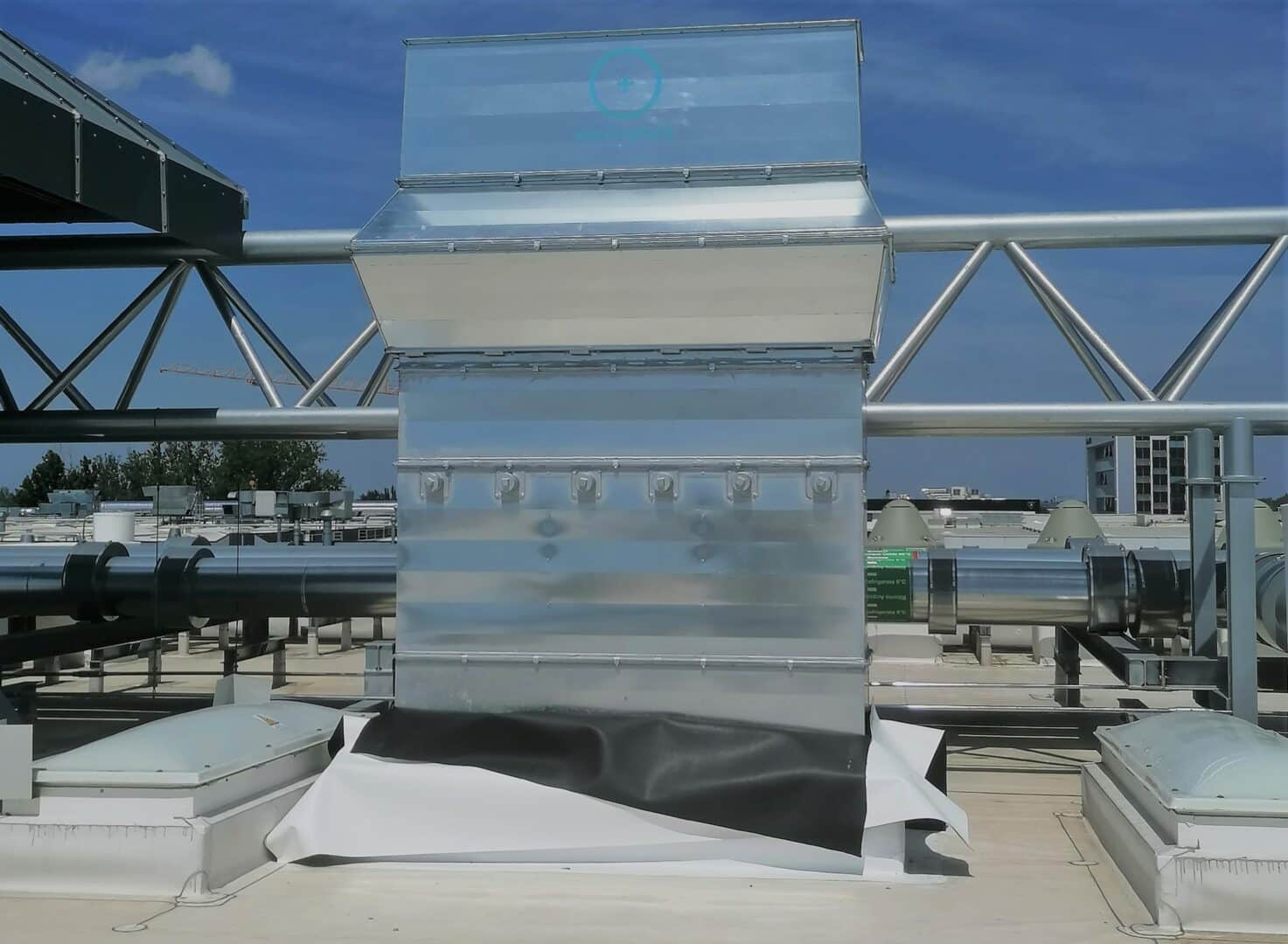
To overcome the difficulties resulting from misalignment of the tracks, our workers developed a thickness gauge system to be used on site to level the tracks of the Laser Guided Vehicles, adjusted according to the roughness of the sheet steel floor.
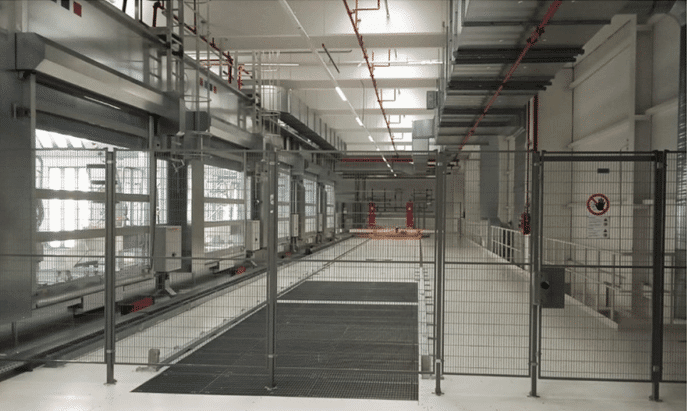
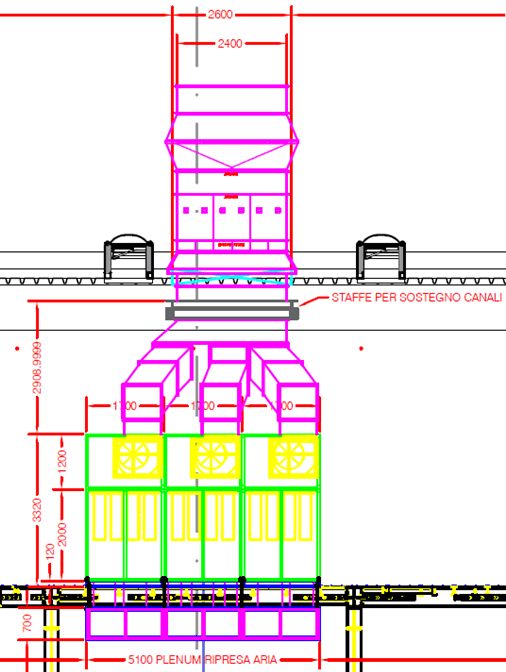
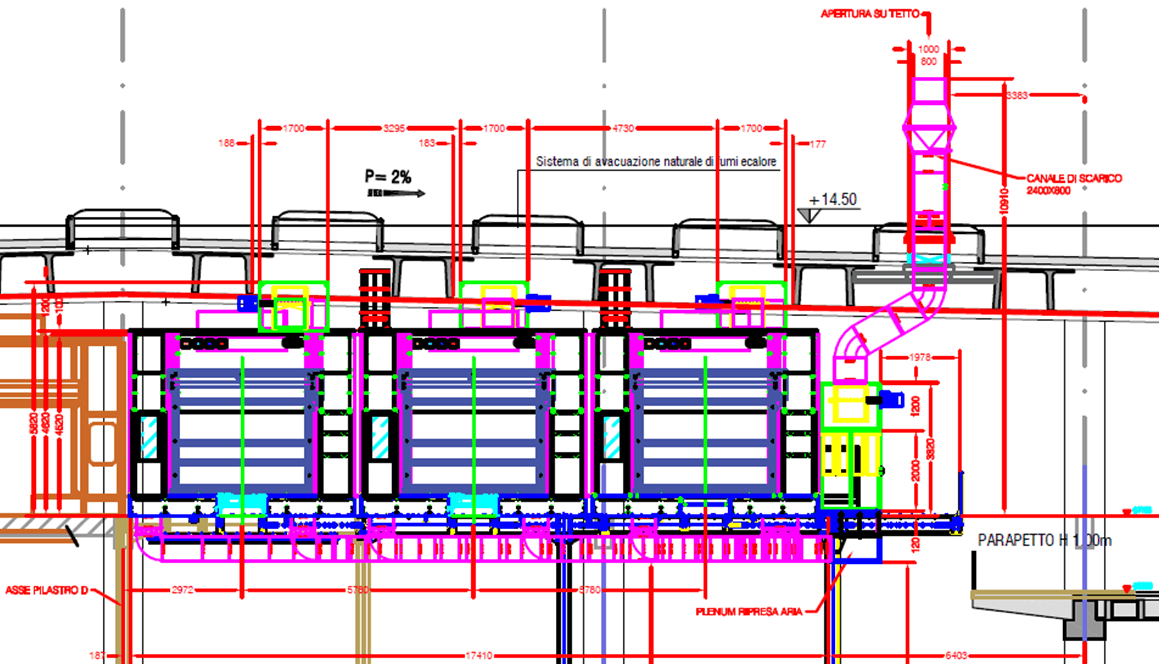
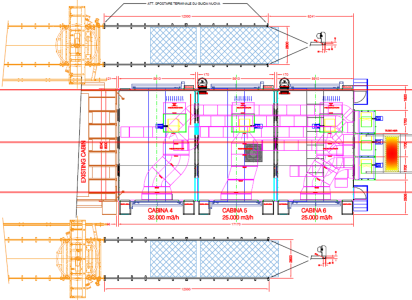
Final results: goals achieved in record times
- Achieving the required quality while respecting design specifications. The paint booths designed and made by Movingfluid for Lamborghini have fully met every requirement, functional and aesthetic, guaranteeing the continuity of the look and feel with the booths made previously by a different supplier.
The tests on the delivered product were carried out by the commissioning company with an external certifier body, appointed by them. The measurements confirmed the effectiveness of the technology and documented the proper ventilation of the workplace.
- Better air circulation. Keeping the construction volumes and the geometry of the previous structures unchanged, the performance of the new paint booths made by Movingfluid exceeded the performance of the previous ones with startling values:
air velocity in booth: +35%
circulated air volume per hour: +35%
- Compliance with environmental standards on emissions into the atmosphere. Installation of specific filters designed to guarantee the appropriate treatment of the fumes emitted by liquid paint products and solvents, containing volatile organic compounds.
- Compliance with deadlines. All the work was done in 6 weeks. System delivered on May 9, 2021, after 42 days of nonstop work in day and night shifts with a team of 18 people who alternated to execute the work in compliance with Covid-19 procedures.
To build the paint booths, Movingfluid engineers worked without interfering in any way with production in progress, adapting their work agenda to company planning, which proceeded without slowing down.
- Zero accidents.
- Setup of the new booths to be integrated with the company IT system, a very important aspect considering the high automation level set by the brand in its processes.
Do you know all the advantages of our solutions?
Discover them here!
Do you need to upgrade your line with a permanent solution but you have little space?
Or perhaps you need to meet temporary peaks in demands, without investing in new buildings?
We can resolve your mishap, in any case!
- Alstom [1]
- ARO Ingersoll Rand [1]
- Automotive [8]
- Brembo [2]
- Case History [13]
- Cast iron brakes [1]
- Ceramic [2]
- Chemical [3]
- chemical mixer [1]
- Chemistry [2]
- Cleaning [1]
- cleaning industrial machinery [1]
- Dilution [1]
- Dosage [4]
- Dust [1]
- Extrusion [3]
- Finishing [1]
- Fluid handling [3]
- Fluids [2]
- Food [1]
- Freni in ghisa [1]
- Gases [3]
- Glue [2]
- Henkel [1]
- Industrial Painting [4]
- IVECO [1]
- Know-how [2]
- Körber Tissue [2]
- Lamborghini [2]
- Liquid paint [1]
- Liquids [6]
- LPR [1]
- Market news [4]
- mixing chemicals [1]
- Nikola [1]
- Oenology [2]
- Oil & Gas [1]
- Paint [2]
- Paper [2]
- Paper converting [1]
- Paper industry [2]
- Powder Coating [1]
- Powders [1]
- pump test bench [1]
- Raw material producer [1]
- Saipem [1]
- Spraying [5]
- Streparava [1]
- SuperSix [1]
- Tissue [3]
- Tissue converting [2]
- Toscotec [1]
- Trail [1]
- Transfer [7]
- Verniciatura industriale [3]