In this article:
-
- Production capacity and the challenge involving all OEM companies
- Automotive and braking systems: an industry at full throttle
- OEMs and brake disc industrial painting. Yes but… how long does curing last?
- Movingfluid and the missing space. One more problem “cured” to perfection!
- Results exceeding expectations. Less space, greater productivity and unexpected savings
Production capacity and the challenge involving all OEM companies
For factories operating at their full production capacity, one of the biggest challenges is optimising the use of space.
Below you can find out how Movingfluid – alongside LPR, Brembo and the Streperava Group – managed to solve the problem at the source through targeted measures within a production process for curing brake discs after their industrial painting. A typical process for the Original Equipment Manufacturers’ market that requires a lot of space.
The lack of available surface to streamline an industrial plant and ensure greater productivity is a problem experienced by many companies. For this reason, upgrading a production line often implies moving machinery to separate factories, not to mention relocating the company itself, involving different departments.
Given the hardship and the costs involved, companies are, therefore, forced to give up on increasing or diversifying production. A real shame when the market does exist and orders arrive.
Another issue that should not be underestimated is the variable flow of demand. OEM spare parts orders, for example, are often affected by seasonal peaks. In the Automotive OEM sector, where industrial painting processes are frequently used, parts can be in growing demand especially in peak periods. If the volume of demand is not guaranteed in the medium to long term, is it really worth investing in a new plant?
Under these circumstances, we are faced with the need to intensify production – sometimes limited to certain periods – and with a lack of additional space: two combined “mishaps”, to say it in a non-technical, but highly human jargon.
This starting condition spurs us, because it gives us the opportunity to lead our customer to win a great challenge. Overturning the situation. Ensuring that an opportunity arises for them from this condition.
We state this because we are specialised in industrial painting, surface treatment, fluid handling. We are thoroughly acquainted with products and processes. In our eyes, a problem is only the door to a solution.
If you need certainty in any fluid handling process,
rely on our engineering consulting services.
Automotive and braking systems: an industry at full throttle
In Italy there are valuable manufacturing companies that supply Automotive OEMs and provide aftermarket services worldwide. A brand of excellence, a feather in the cap of our entrepreneurial fabric, which we had the honour of working alongside by jointly making an important improvement in this sector.
In particular, Movingfluid was the key to trigger production streamlining with a total disruption approach compared to traditional techniques, bringing several advantages including the optimised use of space and unexpected savings in various areas.
The problem experienced by our customers referred in particular to the industrial painting of brake discs, a production process that necessarily requires – as we will see below – defining pre-set spaces to accommodate treated parts waiting for drying.
Given these constraints, in addition to non-compressible spaces and times, what should be leveraged to streamline the production process?
The goals that Movingfluid set itself in its approach to this problem in several directions exceeded customer expectations by aiming at:
- downsizing the overall dimensions of the system
- decreasing the time spent in the furnace and for cooling
- reducing the so-called “parking areas” for parts
- generating energy savings
To streamline the industrial painting processes for brake discs, our engineering firm worked alongside:
LPR: LPR Brakes operates in the global market of automotive parts, dealing with the production of braking systemspare parts.
As a result of its far-sighted management, LPR gained the experience that currently places it at the top of the world market for quality and innovation, and, as a brand established in over 76 countries around the world, became one of the largest aftermarket manufacturers of brake spare parts at an international level.
Brembo: Brembo is a world leader in the design, development and production of braking systems and components for cars, motorcycles and industrial vehicles, for the original equipment, spare parts and racing markets. The company is active on three continents, with 24 factories and commercial sites, and relies on over 11,000 employees.
Streparava: the Streparava Group is among the leaders in the automotive sector and a partner of the most important manufacturers for powertrain, driveline, suspension and engine components and systems. An exclusive partner of the world’s leading automotive brands, the Streparava Group works alongside its customers – car, truck and bus makers among them – throughout the product life cycle including custom development, testing and production.
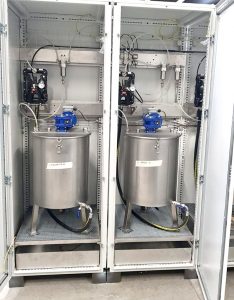
OEMs and brake disc industrial painting. Yes but… how long does curing last?
How does the industrial painting and curing process for brake discs work?
And what about the space needed for brake disc paint curing at the end of the industrial painting treatment?
Let’s get into the heart of the process.
The material commonly used for brake discs is cast iron, except for sports car applications, where carbon ceramic systems are used. In the final step of their production process, brake discs are processed using mostly robot-operated machine tools. If necessary, brake discs are subsequently painted and cured in a furnace.
Through horizontal or vertical hot air ventilated furnaces, powered by gas burners, cast iron brake discs gradually reach the desired temperature.
This is where the main constant of the process comes into play, namely space. During cooling, the treated parts necessarily end up in the marked dimensional areas. Only later can they be handled and packaged to complete the operation.
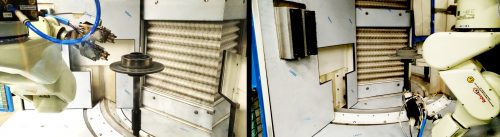
The length of an industrial painting furnace is calculated from the time required for curing parts.
In painting systems, based in particular on water-based paints, parts need to be heated in a hot air furnace on average for 40 minutes/1 hour at a temperature of about 80°C. Large parts, or large-volume ones, require a longer drying time. Only by allowing parts to dry for the time needed can a flawless result be achieved.
So how long does a furnace need to be to accommodate all the treated parts in order for them to get perfectly dried? The calculation is easily done: given that a conveyor belt moves parts forward at a typical speed of about 0.5 m/min., the furnace ought to be 20 to 30 m long.
At the end of the painting process, the absorbed heat needs to be dissipated, an operation that can be carried out in two ways:
- through a tunnel with forced cooling air, requiring additional space, con richiesta di ulteriore spazio
- By placing the painted pieces on the ground, waiting for them to be handled or packed.
Both alternatives generate a further space critical issue..
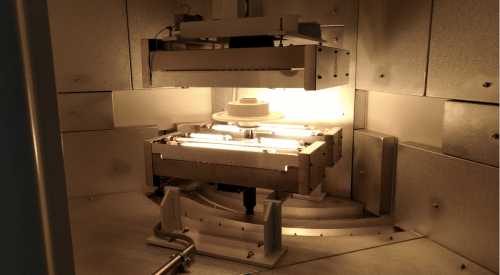
Movingfluid and the missing space. One more problem “cured” to perfection!
As provided by Movingfluid’s method, we took a transparent approach towards the solution.
Therefore, we:
- acknowledged the need expressed by our business partners: to streamline the industrial painting process for brake discs despite the lack of additional space
- collected all necessary data about the plants and processes involved
- identified and shared an appropriate technological solution with the customer
- carried out tests with specific measurements once our partners gave their go-ahead. Data was then recorded and specific documentation produced jointly with the paint manufacturers.
In line with Movingfluid’s solution, the following technologies were used:
- short-wave infrared radiation for paint curing
- an adiabatic process to cool parts
Why was short-wave infrared radiation chosen for paint curing? This technology makes it possible to heat the surface of a part in a short time, without sealing the film of the applied paint, which is a further advantage. In this way, the paint layer can reach temperatures around 100°C very quickly, without generating surface defects such as blistering and burns.
By managing to decrease the dwell time of parts in the furnace to just a few minutes through infrared radiation, it goes without saying that the innermost section of a part remains cold. At this point, cooling the parts will also be faster.
Not only that. To further minimise the time required to complete the process, Movingfluid suggested maintaining an adiabatic thermal condition by means of finely atomised high-pressure water. Together with a forced ventilation system, this treatment ensures further reduced cooling times in confined spaces.
If you want to learn more about this subject, we talked about speeding up the industrial painting and paint curing processes for large surfaces (rail engines) in this case history alongside Alstom Ferroviaria.
.
Results exceeding expectations. Less space, greater productivity and unexpected savings
The results achieved with the proposed solution exceeded the expected milestone, proving how important it is for Movingfluid not only to satisfy the customer, but also to seize all possible opportunities from a condition that at first appeared to be a disadvantage.
The benefits of this revolutionary drying system for cast iron parts after an industrial painting process are as follows
Economic advantages:
- Reduction of energy costs per year: approx. -17%
- Fewer square metres used in the plant: space reduced by approx. 74%, thus successfully eliminating the need to pinpoint new production areas
- Cost cutting as a result of reduced insurance premiums and consequently downgraded risks
Safety:
- Higher degree of safety in the work area, as a result of completely abolishing the use of methane gas, its burners and systems
Technological advantages:
- Use of more cutting-edge, more modular (fine tuning) and controllable technologies
Environment::
- Last but not least – and maybe the first plus ever: the proposed system is environmentally-friendly. A green solution protecting the environment in two ways: by producing less C02 and by drastically cutting down on the use of energy required.
Would you like to know what advantages we could generate in your production process? Movingfluid’s engineering consulting services cover other sectors as well, such as chemistry, oenology, ceramics, cleaning.
A custom solution for every “mishap”.
Would you like to find out more about us before telling us about your problem?
Call us! We can understand each other better by voice!
- Alstom [1]
- ARO Ingersoll Rand [1]
- Automotive [8]
- Brembo [2]
- Case History [13]
- Cast iron brakes [1]
- Ceramic [2]
- Chemical [3]
- chemical mixer [1]
- Chemistry [2]
- Cleaning [1]
- cleaning industrial machinery [1]
- Dilution [1]
- Dosage [4]
- Dust [1]
- Extrusion [3]
- Finishing [1]
- Fluid handling [3]
- Fluids [2]
- Food [1]
- Freni in ghisa [1]
- Gases [3]
- Glue [2]
- Henkel [1]
- Industrial Painting [4]
- IVECO [1]
- Know-how [2]
- Körber Tissue [2]
- Lamborghini [2]
- Liquid paint [1]
- Liquids [6]
- LPR [1]
- Market news [4]
- mixing chemicals [1]
- Nikola [1]
- Oenology [2]
- Oil & Gas [1]
- Paint [2]
- Paper [2]
- Paper converting [1]
- Paper industry [2]
- Powder Coating [1]
- Powders [1]
- pump test bench [1]
- Raw material producer [1]
- Saipem [1]
- Spraying [5]
- Streparava [1]
- SuperSix [1]
- Tissue [3]
- Tissue converting [2]
- Toscotec [1]
- Trail [1]
- Transfer [7]
- Verniciatura industriale [3]